What’s New
Exploring Herbert's Zero Point Clamping System: Enhanced Efficiency and Flexibility in Workholding
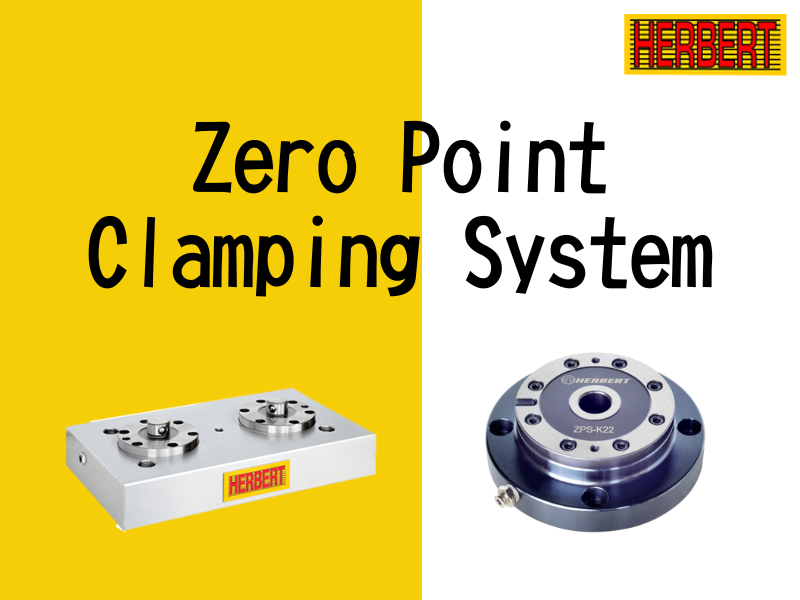
Introduction:
In the realm of workholding solutions, Herbert stands out as a reputable manufacturer that offers innovative and reliable solutions for machining operations. Among their range of products, Herbert's Zero Point Clamping System stands as a key offering, revolutionizing workholding in various industries. This article aims to provide an in-depth understanding of the components and functions of Herbert's Zero Point Clamping System, as well as explore its versatile applications across different industrial sectors.
Components of Herbert's Zero Point Clamping System:
Base Plate:
The base plate is the foundation of the Zero Point Clamping System. It is securely mounted onto the machine table and serves as the anchor for other system components. The base plate incorporates multiple mounting holes or a grid pattern to allow for flexible and precise positioning of workholding elements.
Clamping Module:
The clamping module is a key component of the Zero Point Clamping System. It consists of a receiver and a clamping mechanism. The receiver, mounted on the workpiece or fixture, provides the connection point for quick and accurate clamping. The clamping mechanism, often spring-loaded or hydraulically actuated, ensures a secure and reliable grip on the workpiece.
Zero Point Chuck:
The Zero Point Chuck acts as the interface between the clamping module and the base plate. It contains the clamping pins or balls that engage with the receiver on the clamping module, establishing a precise and repeatable connection. The Zero Point Chuck enables quick and tool-free mounting and dismounting of workpieces or fixtures with minimal setup time.
Pneumatic or Hydraulic Actuation:
Depending on the specific requirements and application, Herbert's Zero Point Clamping System can be operated pneumatically or hydraulically. The actuation system allows for quick engagement and disengagement of the clamping module, enhancing the efficiency of workpiece changeovers and reducing machine downtime.
Function and Benefits of Herbert's Zero Point Clamping System:
- Rapid Workpiece Changeover: Herbert's Zero Point Clamping System enables rapid workpiece changeovers by allowing operators to quickly mount and dismount workpieces or fixtures. This significantly reduces setup time and increases machine utilization, leading to improved overall productivity.
- Precise and Repeatable Positioning: The Zero Point Clamping System ensures precise and repeatable positioning of workpieces. The accuracy of the system allows for consistent results across multiple machining operations, reducing the need for rework and improving overall machining quality.
- Flexibility and Versatility: Herbert's Zero Point Clamping System offers a high degree of flexibility and versatility in workholding. With the ability to mount and interchange various workpieces or fixtures on a single base plate, the system enables efficient multi-part machining and accommodates diverse production needs.
- Enhanced Operator Safety: The Zero Point Clamping System enhances operator safety by minimizing the need for manual handling of heavy or awkward workpieces. The quick and secure clamping ensures a safe and reliable grip, reducing the risk of accidents or injuries during workpiece changes.
Applications of Herbert's Zero Point Clamping System:
- Aerospace Industry: In aerospace manufacturing, where precision and efficiency are critical, the Zero Point Clamping System finds applications in machining complex components such as turbine blades, aircraft structural parts, and engine components.
- Automotive Industry: In automotive manufacturing, the Zero Point Clamping System is utilized for machining engine blocks, cylinder heads, transmission components, and other critical automotive parts, enabling efficient production with rapid workpiece changeovers.
- General Manufacturing: The Zero Point Clamping System is widely employed in general manufacturing for various applications, including milling, drilling, grinding, and turning operations. It provides increased productivity and flexibility, allowing manufacturers to optimize their production processes.
- Tool and Die Industry: The Zero Point Clamping System is extensively used in the tool and die industry for machining dies, molds, and other workpieces requiring precise positioning and repeatable clamping. Its efficiency and flexibility contribute to reduced setup times and increased throughput.
Conclusion:
Herbert's Zero Point Clamping System represents a breakthrough in workholding, providing enhanced efficiency, flexibility, and precision in machining operations. With its carefully engineered components, rapid workpiece changeovers, and versatile applications across industries such as aerospace, automotive, general manufacturing, and tool and die, the Zero Point Clamping System is a valuable asset for manufacturers seeking to optimize productivity and streamline their workholding processes. Incorporating Herbert's Zero Point Clamping System offers manufacturers the ability to achieve consistent results, reduce setup times, and enhance overall machining efficiency. Contact us today to explore the benefits of Herbert's Zero Point Clamping System for your specific machining requirements.