What’s New
What is Zero Point Clamping System and how it works?
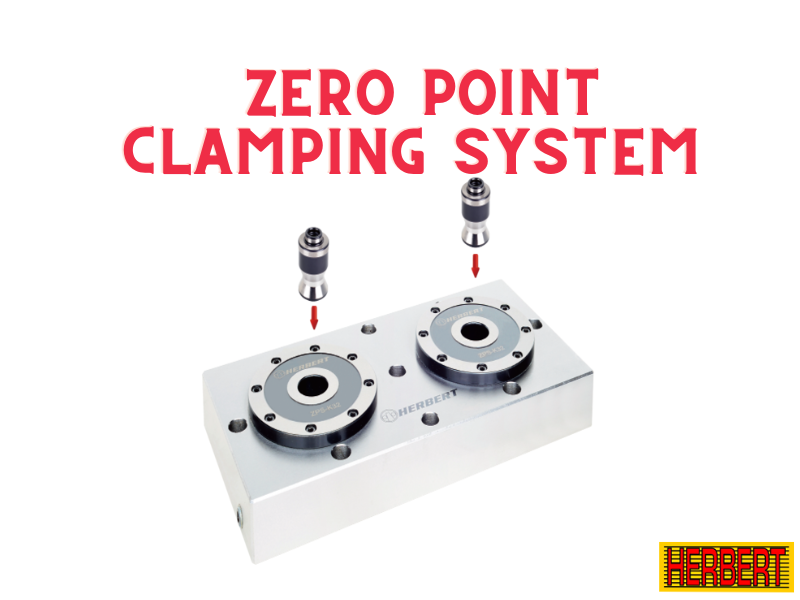
Herbert, a leading manufacturer based in Taiwan, has been focusing on providing innovative and practical solutions for the manufacturing industry. In this article, we will explore in detail one of the most practical solutions that have been developed in recent years, the Zero Point Clamping System. This system is designed to increase productivity, efficiency, and precision in manufacturing.
The Zero Point Clamping System is a modular clamping system that is used in CNC machining, milling, and robotics applications. It operates using the principle of a vacuum seal and is capable of firmly securing the workpiece without the need for any mechanical clamping. The obvious advantage of this system is that it significantly reduces the setup time required for the machine and allows for the workpiece to be changed out quickly and effectively.
The Zero Point Clamping System consists of four components – the base unit, clamping module, clamping pin, and locking mechanism.
- 1. 2. The base unit is mounted on the machine table and the clamping module is commonly attached to the workpiece.
- 3. The clamping pin is used to engage with the clamping module, which creates the air-tight seal that holds the workpiece in place.
- 4. The locking mechanism is used to secure the clamping pin in place, ensuring the workpiece remains firmly held.
One key benefit of this system is its ability to increase manufacturing efficiency. Compared to traditional clamping methods, the Zero Point Clamping System can reduce setup time by up to 90%. Since the clamping is done pneumatically, there is no time-consuming process of screwing and unscrewing clamps. In addition, there is no need to re-indicate the workpiece after it is reset, because the position of the fixture is precisely located by the Zero Point Clamping System.
The Zero Point Clamping System also contributes to an increase in machine runtime. With a faster setup time, it enables machining centers to operate with greater flexibility. The reduction in setup time also means that more parts can be p rocessed in less time, leading to an increase in productivity and throughput. This is ideal for high volume production runs.
Another advantage of the Zero Point Clamping System is its accuracy. The system provides a repeatable and precise way to position workpieces, which is essential for achieving consistent quality and accuracy in parts. The system adds to the machine tool's accuracy by positioning the part precisely in relation to the tooling station. The system's accuracy can be improved even further with the use of the clamping module, as it secures the part easily, safely, and accurately.
The precision of the Zero Point Clamping System also leads to an improvement in part quality. Because of the system's accuracy, it is possible to achieve tight tolerances, which cannot be attained through traditional clamping methods. This is critical for industries such as aerospace, medical, and automotive, where precision is paramount.
The Zero Point Clamping System helps minimize the risk of distortion and damage to the workpiece. The system achieves this by exerting uniform force on the workpiece, avoiding the risk of distortion, which can occur with traditional clamping methods. This characteristic is especially important when working with delicate or complex parts, where distortion or damage could mean a significant loss of resources.
The Zero Point Clamping System also contributes to cost reduction. The elimination of manual clamping saves time, and better accuracy leads to less wasted material. With higher accuracy, fewer parts would need to be reworked, which means no wasted labor and material, resulting in both time and cost savings.
Finally, Herbert's Zero Point Clamping System is extremely versatile. It has a wide range of applications, from small to large workpieces, simple to complex shapes, and can be used with various manufacturing processes. It is compatible with a range of materials—metals, composites, plastics, and even fragile materials such as glass.
In conclusion, the Zero Point Clamping System is an innovative solution that is transforming the manufacturing industry. Its advantages in terms of efficiency, precision, accuracy, and cost reduction make it a vital tool for companies that seek to stay ahead of the competition. Its versatility and ease of use make it an ideal solution for manufacturers in diverse industries, and with continuous development by Herbert, it will continue to shape the manufacturing industry for years to come.
Q1: What is a Zero Point Clamping System and how does it benefit manufacturing processes?
A1: A Zero Point Clamping System is a sophisticated fixture system used primarily in CNC machining and other manufacturing settings to enable rapid and precise positioning and changing of workpieces and fixtures. The system operates on a mechanism that uses pre-defined reference points, or 'zero points', allowing operators to quickly set up or change equipment with minimal alignment issues. This significantly reduces setup times, enhances repeatability, and improves overall machining accuracy, thereby boosting production efficiency and reducing operational costs.
Q2: How does the Zero Point Clamping System integrate with Quick Change Systems to optimize production lines?
A2: The Zero Point Clamping System complements Quick Change Systems by further streamlining the changeover process in manufacturing environments. When integrated, these systems allow for even quicker swaps of tools, dies, and fixtures with extremely high precision. This integration is particularly effective in high-mix, low-volume production scenarios where frequent setup changes are common. By minimizing the time and effort required for each change, these systems collectively enhance the flexibility of production lines, enabling manufacturers to quickly adapt to new or changing production demands without sacrificing quality or efficiency.