What’s New
5 Types of Jaws for Self-Centering Vises: How to Choose the Right One for Your Application
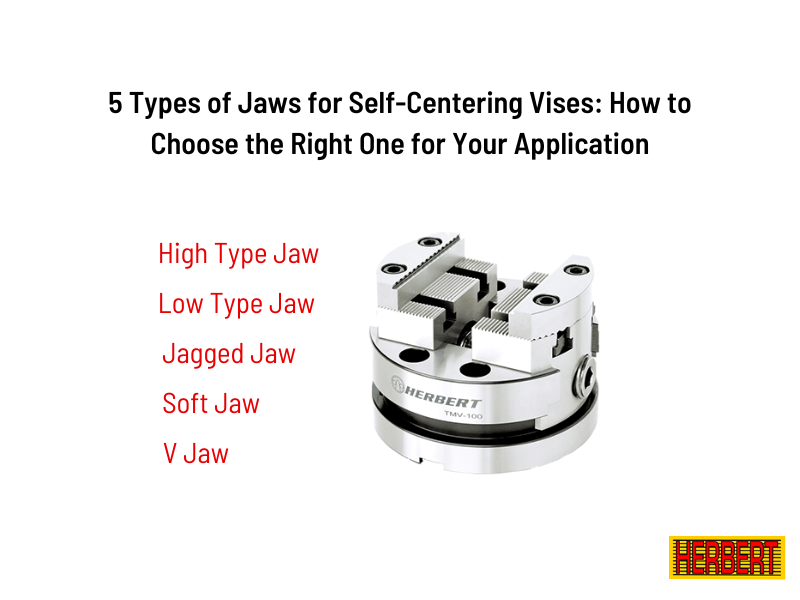
In precision machining, a self-centering vise is a valuable tool that enhances accuracy and efficiency. This type of vise automatically adjusts to position the workpiece at the center, ensuring that each setup is perfectly aligned. Self-centering vises are essential for applications where symmetry and consistency are critical, such as in CNC machining, metalworking, and various assembly processes. One of the key features of self-centering vises is their compatibility with different types of jaws, each serving a unique purpose. In this article, we’ll explore five types of jaws compatible with self-centering vises—high type jaw, low type jaw, jagged jaw, soft jaw, and V jaw—and how to select the right jaw type for your application.
What is a Self-Centering Vise?
A self-centering vise is designed to automatically center workpieces, making it ideal for operations requiring high precision. Unlike standard vises, which require manual adjustments, a self-centering vise uses a mechanism to ensure that the workpiece remains centered regardless of its size. This feature makes it especially useful in CNC milling, where maintaining a consistent center point is essential for producing accurate and repeatable results. Self-centering vises are also widely used in tasks that involve rotational symmetry or require multi-sided machining, as they allow for precise positioning and repeatability across multiple setups.
Applications of Self-Centering Vises
Self-centering vises are used in a wide range of applications, including:
- CNC Machining: Ensures precise alignment for complex parts with symmetrical features.
- Metalworking: Offers stability and precision when cutting or grinding workpieces.
- Assembly Processes: Holds parts accurately in place, ideal for tasks that require exact positioning.
- Inspection and Measurement: Enables repeatable positioning for quality control and testing.
- Woodworking: Used to hold symmetrical wood pieces in place for accurate cutting and drilling.
The versatility of self-centering vises makes them suitable for numerous industries, including automotive, aerospace, electronics, and medical device manufacturing. Each application may call for different jaw types, depending on the material, shape, and stability required for the workpiece.
The 5 Types of Jaws for Self-Centering Vises
The choice of jaw type is crucial in ensuring the vise’s performance matches the specific needs of the workpiece and machining process. Here’s a breakdown of the five types of jaws and how to choose the right one for your application:
1. High Type Jaw
High type jaws are ideal for holding taller or larger workpieces securely. They offer greater surface area for clamping and provide more vertical support, which helps to stabilize large parts during machining. This jaw type is beneficial when working on parts that have a considerable height, as it allows for better grip and reduces the risk of slippage.
- Best for: Tall workpieces, large components that need additional clamping height.
- Applications: Metalworking, CNC milling of larger parts.
2. Low Type Jaw
Low type jaws are designed for clamping shorter or smaller workpieces close to the vise base. They provide stability and minimize the distance between the clamping area and the work surface, which is particularly useful for low-profile machining tasks. This jaw type allows for increased accuracy when working with compact parts and offers better visibility of the workpiece.
- Best for: Short, low-profile workpieces.
- Applications: CNC machining, precision grinding, inspection setups.
3. Jagged Jaw
Jagged jaws have serrated edges that offer an enhanced grip on the workpiece. These jaws are particularly effective for holding rough or irregularly shaped materials, as the serrations “bite” into the material, preventing it from shifting during machining. Jagged jaws are ideal for jobs requiring a secure hold on tough materials that might otherwise slip or move.
- Best for: Irregularly shaped or rough materials, heavy-duty clamping.
- Applications: Roughing operations, heavy-duty CNC machining, metalworking.
4. Soft Jaw
Soft jaws are made from softer materials, such as aluminum or mild steel, that can be machined to fit the exact shape of the workpiece. These jaws are highly customizable, allowing operators to create a form-fit around the workpiece. Soft jaws are ideal for delicate materials or precision components that could be damaged by harder jaws.
- Best for: Delicate or precision components that require a custom fit.
- Applications: Custom machining, delicate workpieces, specialized components.
5. V Jaw
V jaws are designed with a V-shaped groove that enables them to hold round or cylindrical workpieces securely. This design helps to position round parts precisely at the center of the vise, making it ideal for machining or drilling operations that involve cylindrical shapes. V jaws are particularly useful for tasks where the part needs to be centered with high accuracy.
- Best for: Round or cylindrical workpieces.
- Applications: Turning, drilling, CNC machining of pipes and shafts.
Choosing the Right Jaw Type
When selecting the right jaw type for your self-centering vise, consider the following factors:
- Shape and Size of the Workpiece: High type jaws are suitable for taller workpieces, while low type jaws work best for shorter ones. V jaws are ideal for cylindrical objects.
- Material Type: Jagged jaws are recommended for tougher materials requiring a firm grip, while soft jaws are better suited for delicate or customized components.
- Machining Requirements: If the operation requires heavy-duty clamping, jagged jaws offer a better hold. For custom applications or fragile parts, soft jaws provide a more gentle, form-fitting clamp.
- Application Environment: Consider the level of precision and stability needed. For high-precision tasks, a customized fit with soft jaws or a stable grip with high type jaws may be essential.
Conclusion
Self-centering vises offer a versatile and efficient solution for holding workpieces securely, with minimal setup adjustments. The choice of jaw type is critical in achieving the desired clamping strength, stability, and accuracy needed for your application. By understanding the unique functions of high type, low type, jagged, soft, and V jaws, manufacturers can optimize their machining processes, reduce setup times, and ensure consistent quality.
Herbert Enterprise Co., Ltd. provides a range of high-quality self-centering vises and jaw options designed to meet the specific needs of modern machining environments. For more information or to discuss the best vise and jaw configuration for your application, visit our website or contact our team today. We're here to help you find the perfect solution for your precision machining needs.