What’s New
How to Choose the Right Self-Centering Vise for Your Machining Needs
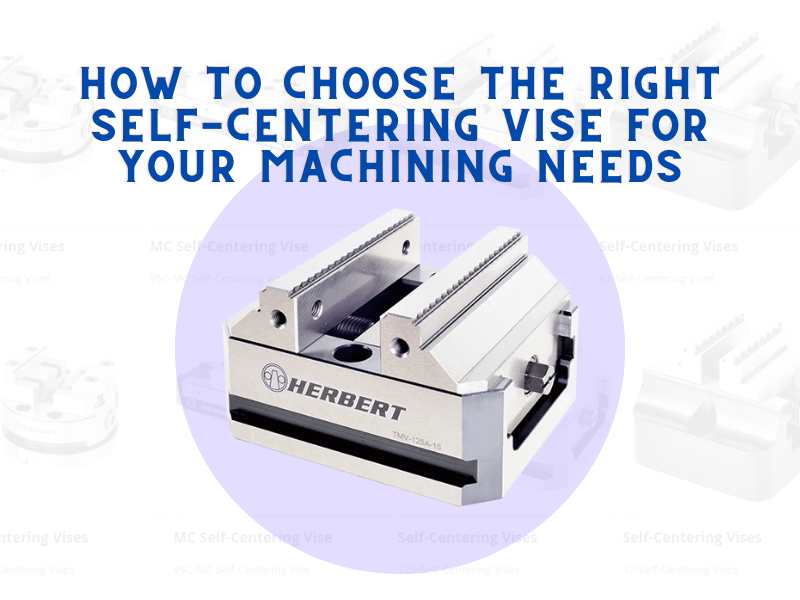
In precision machining, selecting the right self-centering vise can significantly impact the efficiency, accuracy, and overall productivity of your operations. Self-centering vises are designed to ensure automatic and precise alignment of workpieces, eliminating the need for manual adjustments and reducing setup time. But with various options available, how do you choose the best self-centering vise for your specific needs? In this article, we’ll break down the essential factors to consider when selecting a self-centering vise and provide tips to make the best choice for your machining applications.
1. Understand Your Machining Application
The first step in selecting the right self-centering vise is to clearly define your application. Different machining tasks require different levels of precision, stability, and flexibility. Consider the following applications:
- CNC Milling: Requires high-precision clamping and the ability to hold complex workpieces for multi-axis machining.
- Drilling and Tapping: Needs a vise that can securely hold parts during vertical operations.
- Metalworking and Grinding: Demands a robust vise that can withstand high clamping forces and vibrations.
- Inspection and Quality Control: Requires precise and repeatable positioning for accurate measurements.
Understanding your specific machining process will guide you in selecting a vise that can handle the required precision, stability, and flexibility.
2. Consider the Size and Shape of Your Workpieces
Workpieces come in various sizes and shapes, and your vise needs to accommodate these variations. Consider the following factors:
- Workpiece Dimensions:
Ensure that the vise can handle the maximum size of the workpieces you typically machine. Check the jaw opening capacity, overall width, and depth of the vise.
- Workpiece Shape:
- For rectangular or square parts, a standard self-centering vise will suffice.
- For cylindrical parts, opt for a vise that supports V-shaped jaws to ensure a secure grip.
- For complex or custom shapes, consider using soft jaws that can be machined to match the workpiece contours.
Choosing a vise that matches the size and shape of your workpieces will ensure better clamping performance and accuracy.
3. Jaw Types and Their Importance
The jaws on a self-centering vise play a crucial role in determining how securely the workpiece is held. Here are five common types of jaws and their applications:
1. High Type Jaws:
- Best for: Tall or large workpieces requiring extra clamping height.
- Application: Milling or drilling large components.
2. Low Type Jaws:
- Best for: Short, low-profile workpieces.
- Application: Surface grinding, precision milling, and inspection.
3. Jagged Jaws:
- Best for: Rough or irregular surfaces requiring extra grip.
- Application: Heavy-duty machining, rough cutting, and forging.
4. Soft Jaws:
- Best for: Delicate or custom-shaped workpieces.
- Application: Prototyping, custom machining, and fragile materials.
5. V Jaws:
- Best for: Cylindrical workpieces like pipes or shafts.
- Application: Drilling, turning, and milling round components.
Choosing the right type of jaw ensures your self-centering vise performs optimally for your specific machining tasks.
4. Material and Build Quality
The durability and performance of a self-centering vise depend on the quality of materials used. Key considerations include:
• Body Material:
o Cast Iron (FCD60 or higher): Offers excellent durability and resistance to deformation under high clamping forces.
o Hardened Steel: Provides superior strength for heavy-duty applications.
• Surface Hardening:
Look for vises with hardened slideways (HRC45 or higher) to ensure longevity and resistance to wear.
• Corrosion Resistance:
If you work in humid environments or with materials prone to oxidation, opt for vises with anti-corrosion coatings.
Investing in a high-quality vise ensures reliability, longevity, and consistent performance, even under demanding conditions.
5. Precision and Tolerance Requirements
For high-precision applications, pay attention to the vise’s accuracy and repeatability. Check for:
- Centering Accuracy: High-quality self-centering vises offer centering accuracy within ±0.01mm or better, ensuring precise alignment.
- Repeatability: The ability to repeatedly position the workpiece accurately is critical for batch production and quality control.
Choosing a vise with tight tolerances and high repeatability helps maintain consistent quality and reduces the risk of errors during machining.
6. Compatibility with Machine Tools
Ensure the self-centering vise is compatible with your existing machine tools. Consider:
- Mounting Options: Check if the vise can be mounted on your CNC milling machines, lathes, or vertical machining centers. Some vises offer universal mounting options for greater flexibility.
- Quick Change Systems: If your operations require frequent changeovers, look for self-centering vises that integrate with quick change systems. This combination reduces downtime and boosts productivity.
7. Ease of Maintenance
Regular maintenance extends the lifespan of your self-centering vise. Choose a vise with features that simplify maintenance, such as:
- Accessible Components: Easy-to-remove jaws and accessible internal mechanisms make cleaning and maintenance easier.
- Lubrication Points: Built-in lubrication points help keep the vise operating smoothly, reducing wear and tear.
Conclusion
Choosing the right self-centering vise involves understanding your machining needs, selecting the appropriate jaw type, and ensuring compatibility with your machine tools. By considering factors like workpiece size and shape, material quality, precision requirements, and ease of maintenance, you can select a vise that enhances your productivity and machining accuracy.
At Herbert Enterprise Co., Ltd., we offer a wide range of self-centering vises designed to meet the highest standards of precision and durability. Our vises are compatible with various jaw types, allowing you to customize them for your specific applications. For more information or to explore our product offerings, visit our website or contact our customer support team. We are committed to providing the best workholding solutions to help you achieve manufacturing excellence.